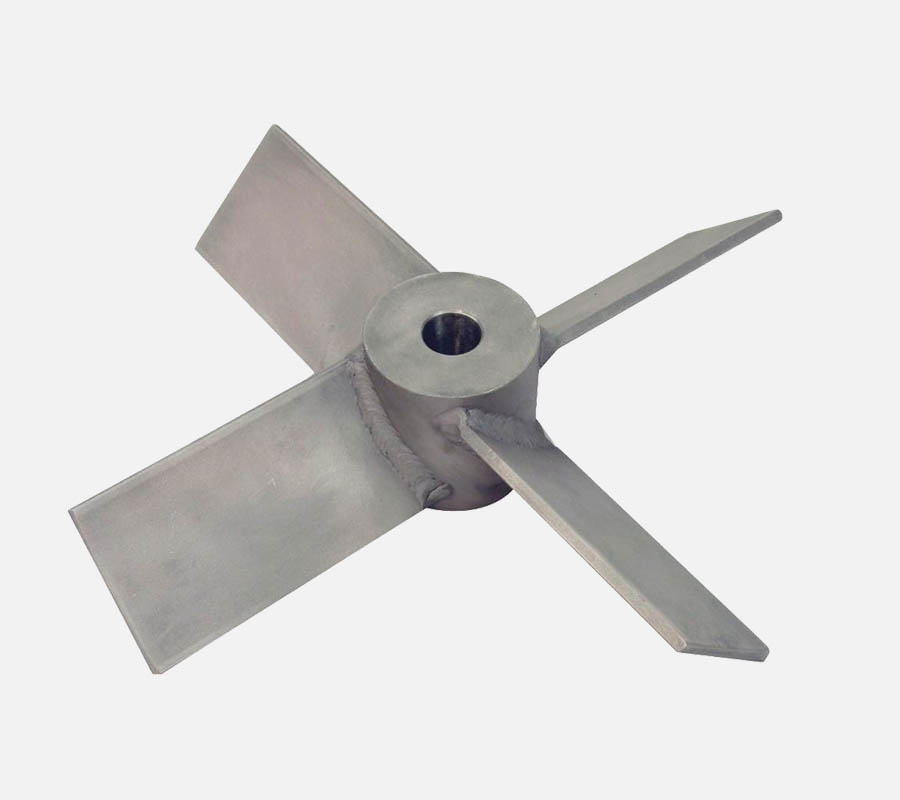
Propeller
These are most common mixed flow (axial & radial) impeller. It is recommended for mixing of two or more low viscous liquid together. It provides effective liquid mixing solution. Mostly available in three blade version. Due to low manufacturing cost of this impeller it gives best economical solution to customer with less manufacturing time.
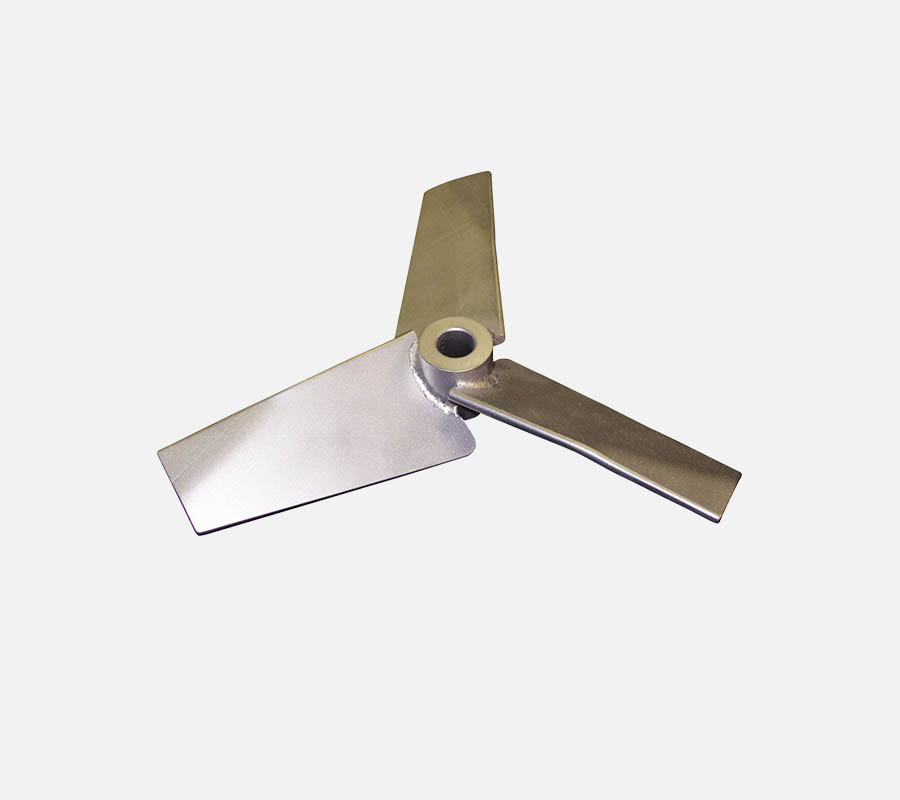
Hydrofoil
These are most efficient axial flow impeller. It is recommended for blending, solid suspension, heat transfer etc. It provides maximum flow at minimum power. Mostly available in three blade version. But different number & width of blade are also common in special applications. This is also called as fabricated propeller.
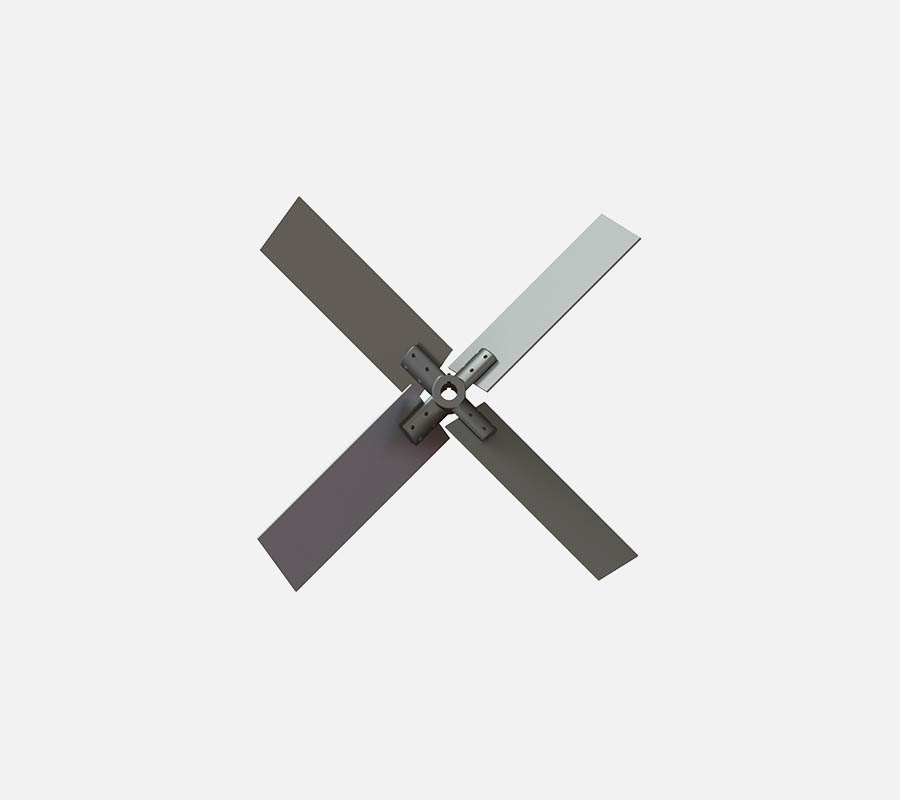
Pitch blade Turbine
These are axial flow impellers with a considerable amount of radial flow. It produces suction when placed near the liquid surface. Hence used for blending of immiscible liquids, solid incorporation etc. It is also a preferred choice for applications where the viscosity change during the process is large. These are mostly available in four blade @ 45 degree. But different no of blade with various angles are also used depending on application.
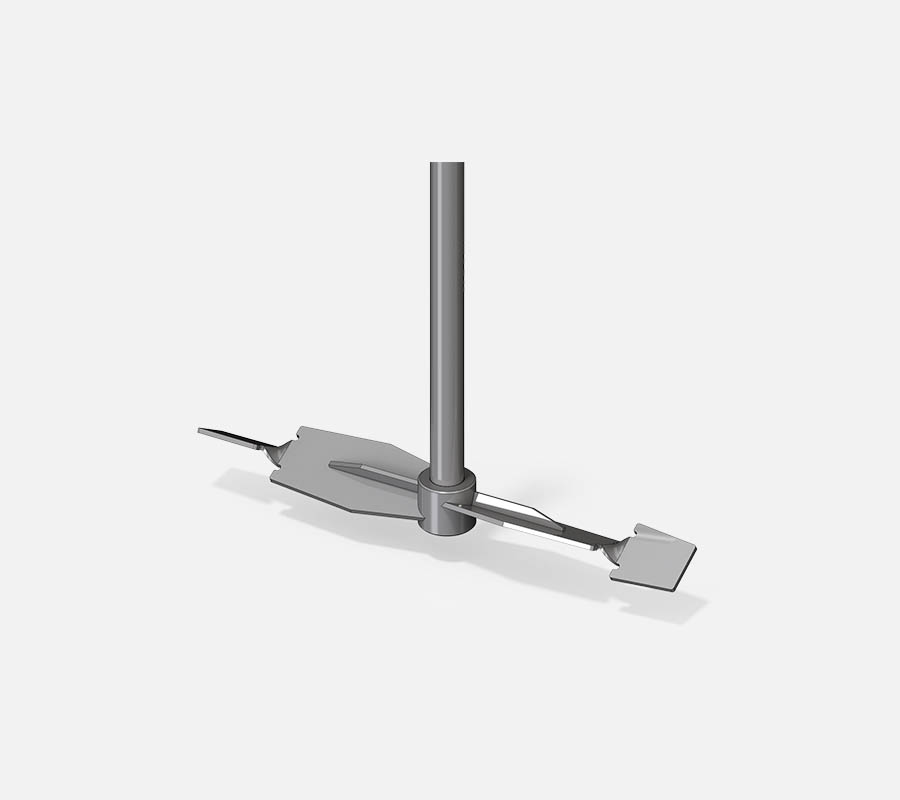
Counter Flow
Flow generated by impellers tip is opposite to the bulk flow produced by the central part. In many case where the slurry fluidity reduces due to high solid concentration. Tip of the impeller provides momentum to the fluid near vessel wall. These are mainly used for slurry with high solid concentration. It efficiently operates at much higher impeller to tank diameter ratio and have higher flow capacity than conventional impellers.
In many application, flow regime is not same throughout the process. It changes from turbulent to transition and even laminar flow in many application. This is most efficient impeller system in such application. It has capability to mix Newtonian as well as Non-Newtonian fluids.
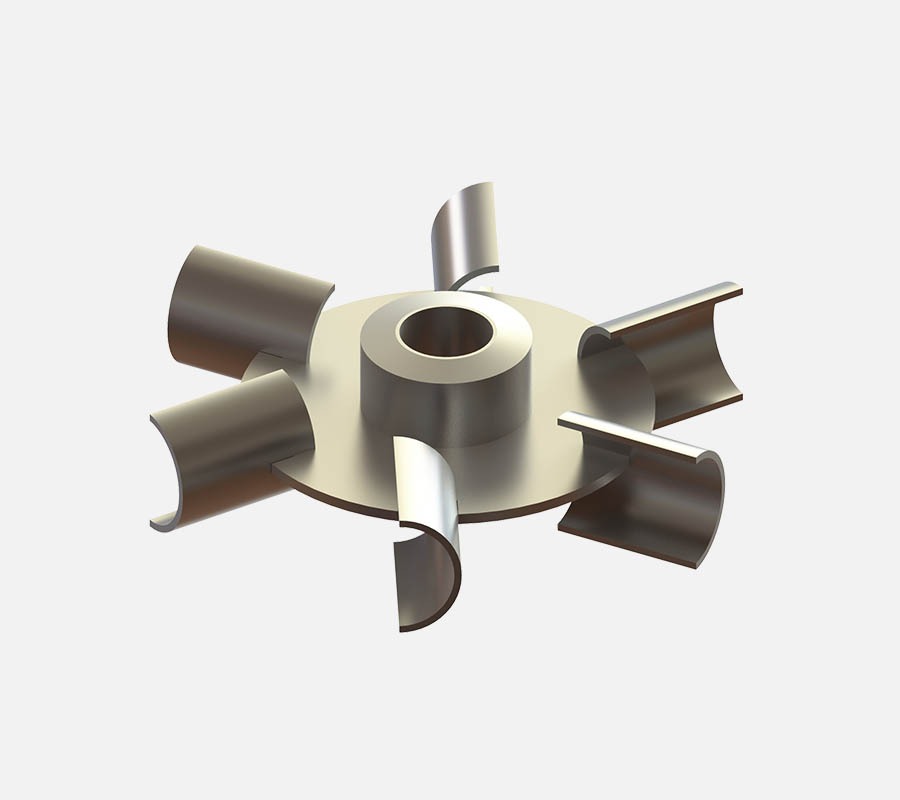
Smith Turbine Impeller
Mostly used for gas dispersion application. Curve blade (Concave, parabolic etc.) disc can handle 2 to 6 times more gas than flat blade disk turbine. Power drop between gassed and un-gassed condition is very less than conventional flat blade disk impellers. Hence it is preferred choice for gas dispersion applications viz. Fermentation, Hydrogenation, Oxidation, Carbonization, Ethylation etc.

Single/Double Helical Ribbon Agitators
Helical ribbon impellers are designed especially axial and overall movement of the liquids. Such an impeller can be designed with an additional inner helix or auger used to pumping in the opposite direction. This is needed for the mixing of high viscosity materials. These impellers can also have one or two start helix. The quality of the final mixed product in these applications are very critical. Wall scrapers can be mounted on the impeller blades to improve heat transfer and homogeneity in sticky products.
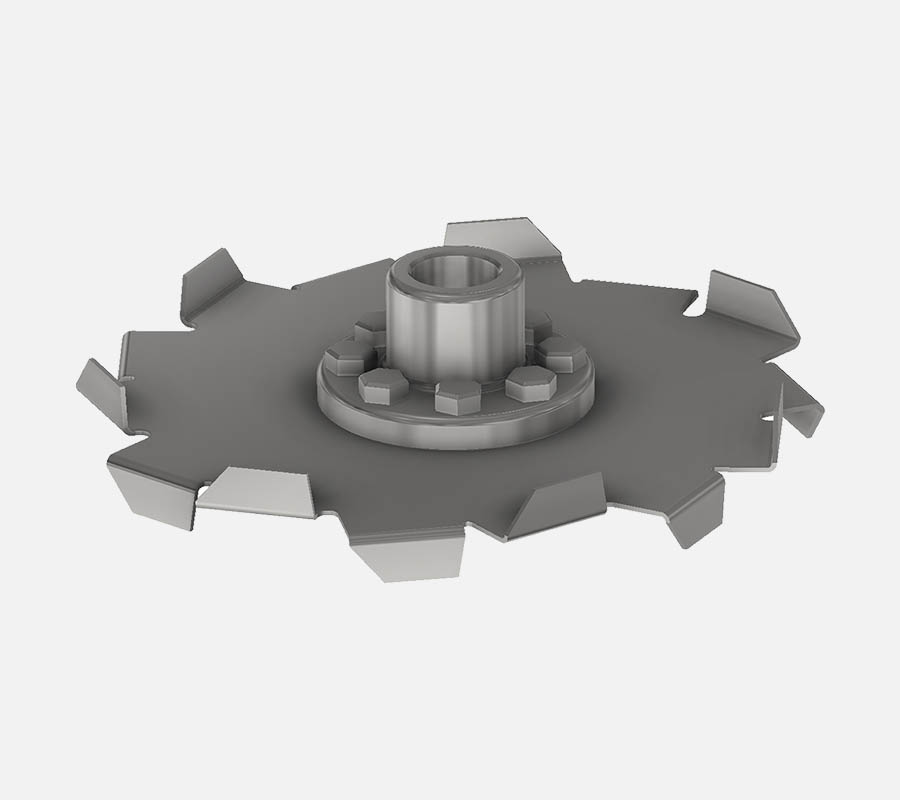
Shear blade Impeller
Disperser disk provides large amount of shear and mostly used for liquid-liquid dispersion, powder dissolution or de-agglomeration etc. Commonly in this type of impeller application shaft is directly coupled with Motor to achieving the high RPM to generate effective shear between liquid.
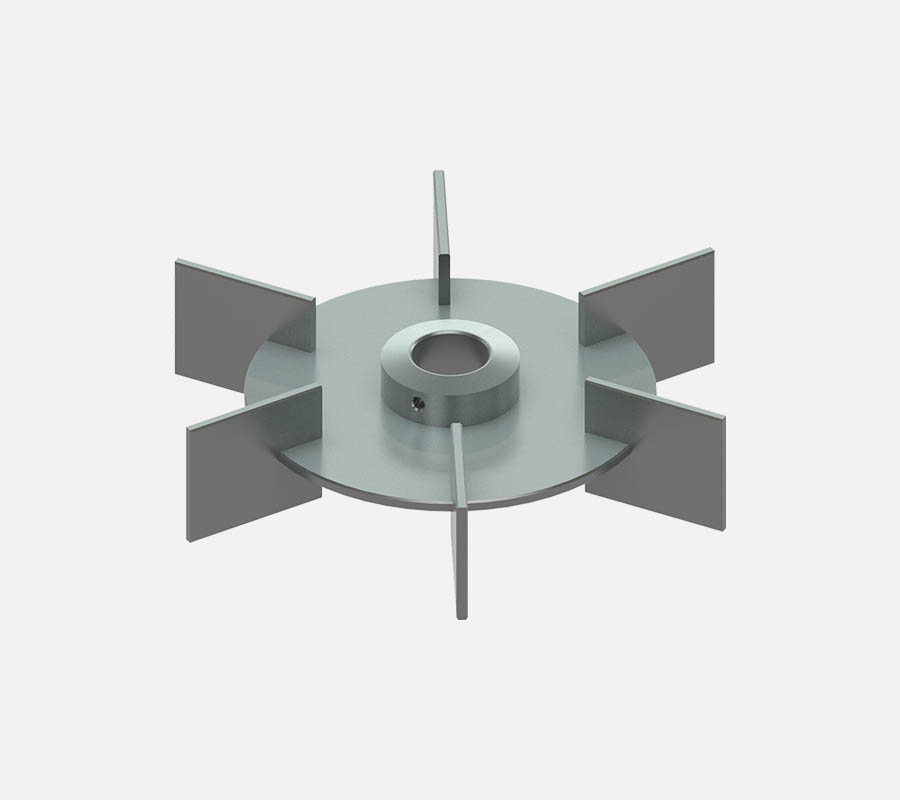
Ruston Blade Impeller
The Rushton turbine is mainly used because of its extensive centrifugal effect for the dispersion of gas/liquid. This dispersion fosters the gas/liquid exchange for processes such as aerobic fermentation. It can also be found in special applications such as stripping type processes.
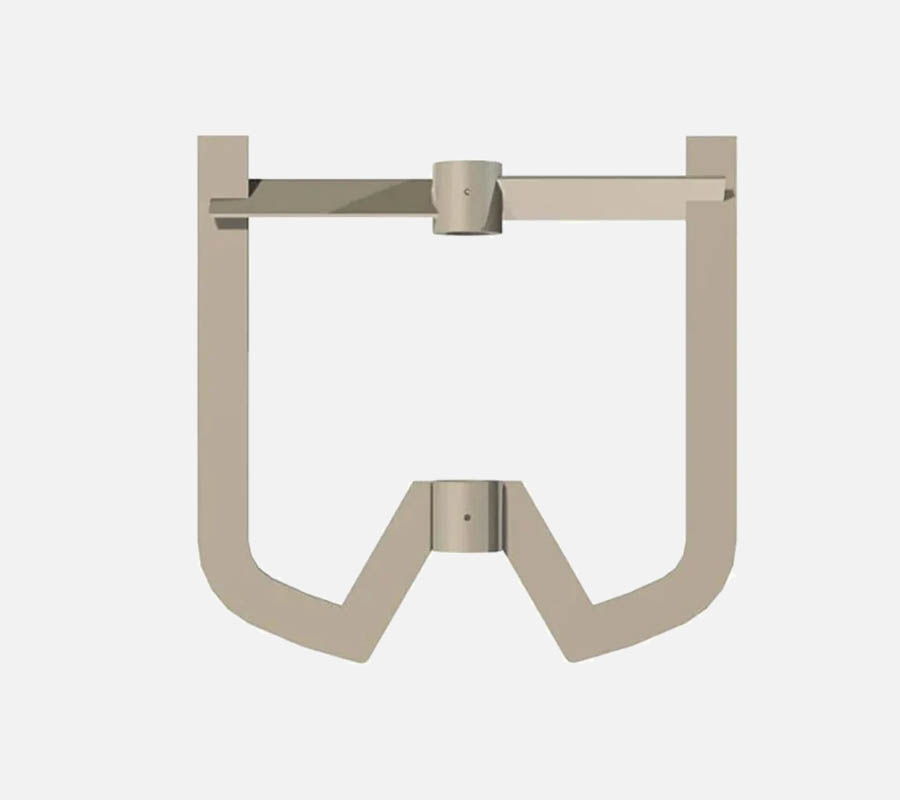
Anchor Type Impeller
Anchors/Gate type impellers are close-clearance impellers that fit the contour of the vessel. These impeller provide adequate mixing under the laminar flow conditions encountered in high viscosity applications for heat transfer. There are many applications that other type of impellers are integrated with the anchor. These impellers sweep the whole wall surface of the vessel and agitate most of the fluid batch through physical contact. Anchor impellers are used for liquid viscosities between 5,000 and 50,000 cP. When reaction/mixing homogeneity is required, other type of impellers are recommended.
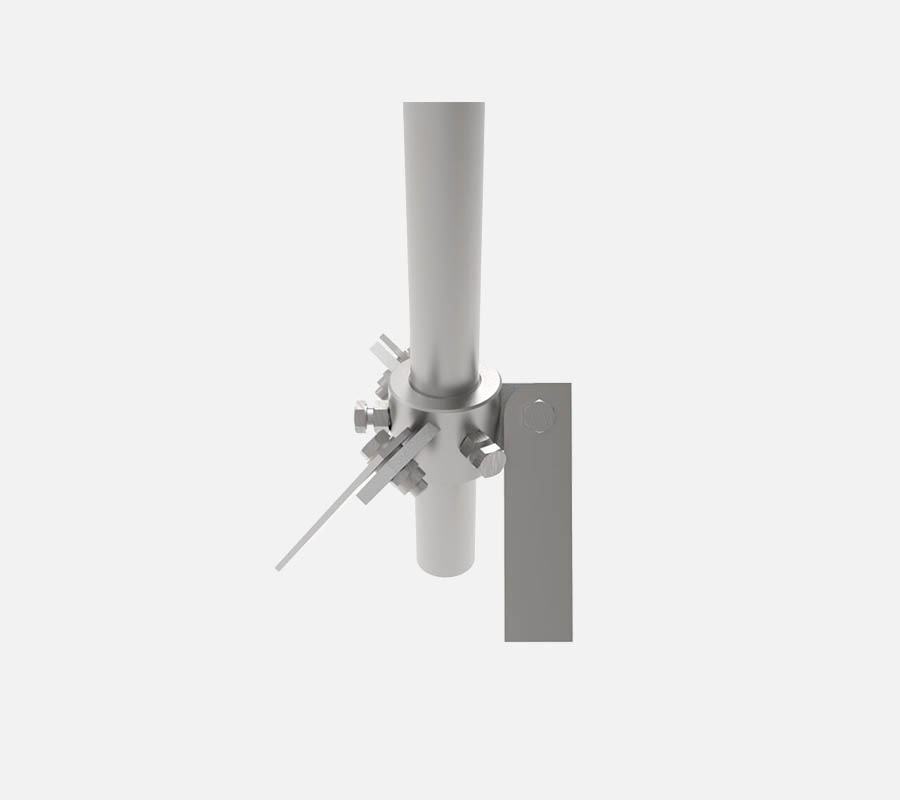
Customized Impeller
We are also Provide Customized impeller design which depends on process requirement. We Dosimix Technologies consistently works on research & development of the Agitator Impeller design using Practical exercises, Computerized Flow simulation & analysis software to improve the blade efficiency for improvement of mixing efficiency with least cost & time.
In addition to our high-quality products, we also offer a range of services to ensure that our clients get the best value for their investment. Our services include installation, commissioning, training, and after-sales support. Our team of experienced engineers and technicians is available to provide assistance and support throughout the product lifecycle.
CFD Simulation Of Agitator Impellers
CFD simulations can help our design engineers to optimize the performance of agitators by predicting key parameters such as power consumption, mixing time, and flow patterns. The simulation results can be used to optimize the design of the agitator and minimize the energy required for mixing.
We have use to conduct CFD simulations for agitators, specialized software such as ANSYS Fluent, ANSYS CFX and Autodesk CFD. These software packages provide a wide range of modeling capabilities and can simulate a variety of flow phenomena.
CFD simulations for agitators typically involve modeling the fluid flow and heat transfer within the tank, including the interaction between the fluid and the agitator blades. The simulation results can be used to optimize the design of the agitator blades, as well as the location and orientation of the agitator in the tank.
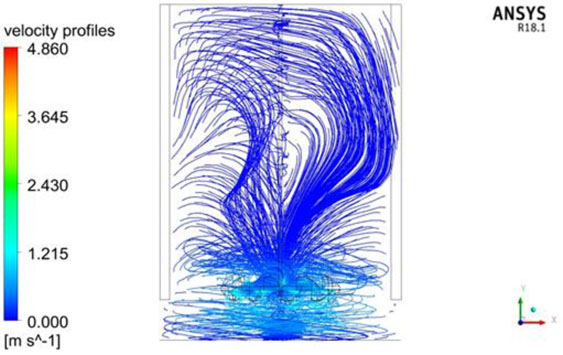
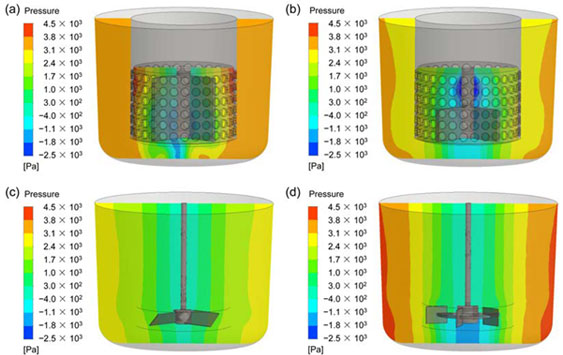
Overall, CFD simulations for agitators can provide us valuable insights into the mixing performance of the agitator, which can help our design engineers optimize the performance and energy efficiency of the equipment.